Manson and Greenberry: Turning Vision into Reality
- J.Anthony Tedpahogo
- Mar 20
- 3 min read
Updated: Mar 21
A successful marine construction project is a collaboration between talented teams who bring complex concepts to life while meeting client expectations. Manson’s Lake Washington Ship Canal (LWSC) Large Lock Center Miter Gate Replacement project exemplifies this spirit of teamwork.

The two-year, $18-million endeavor to replace the century-old miter gate for the United States Army Corps of Engineers (USACE) was made possible through the strong partnership between the client, Manson, and its subcontractors. The fabrication of the new miter gates, in particular, was bolstered by a strong partnership with metal fabricator Greenberry Industrial (Greenberry) out of Vancouver, WA.
“The collaboration between Manson and Greenberry was instrumental in preparing for this massive undertaking,” says Zach Mendenhall, Greenberry Vancouver Facility Manager. “The collective commitment of both teams played a crucial role in the project’s success.”
Zach, a seasoned professional with two decades at Greenberry, reflects on the seamless collaboration between Manson and Greenberry during the design phase—a pivotal stage that set the tone for the entire project.
“Once Manson secured the contract in late 2022, Greenberry was brought in immediately to initiate discussions on design planning,” Zach recalls.
Although he officially joined the project in April 2023—four months into planning and design—Zach quickly noticed the open communication and mutual respect between team members. He knew this project was unique.
“Working alongside Manson Project Manager Kelli Struett and Project Engineers Kurtis Jackson and Madeline Brisson felt like being part of a unified team rather than simply a contractor fulfilling obligations under a watchful eye,” he says.
A key component of the project’s success was the collaborative effort during the prefabrication process. The team dedicated extensive time to drafting and approving shop drawings, carefully addressing inconsistencies and conflicts along the way.
“Manson, Greenberry, and USACE met weekly for months to navigate challenges and propose changes,” Kelli explains. “Every team member involved played a role in evaluating decisions and fully understanding the ripple effects of design changes during fabrication.”
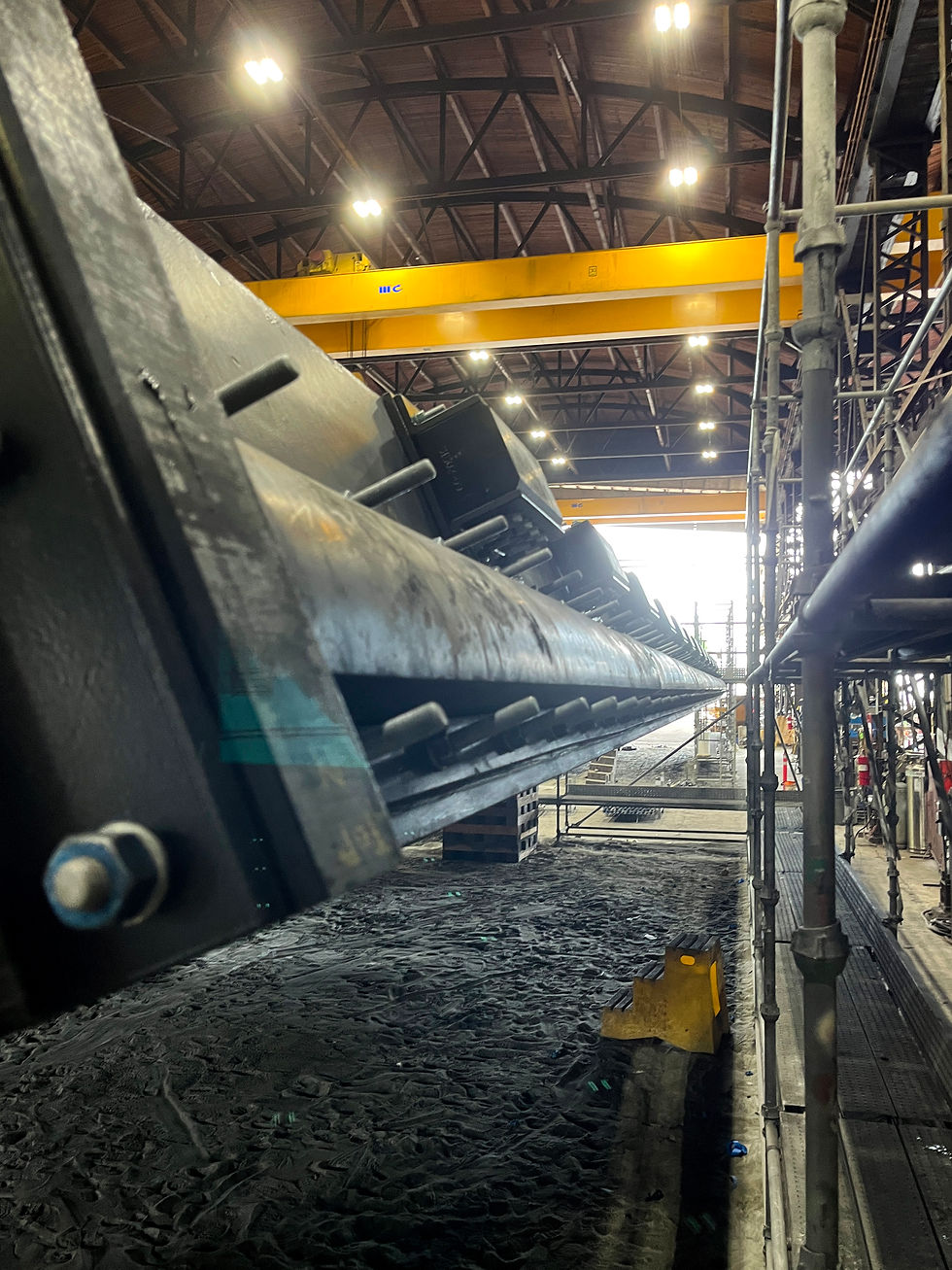
Recognizing the scale of this undertaking, Zach spent months—concurrent with design planning—assembling a skilled team of foremen, fitters, and welders, ensuring they were deeply involved in the build plan.
Following months of deliberation, adjustments, and final approvals, Greenberry received the green light to begin fabricating the new gates and additional components.
“At peak production, we had about 33 fabricators working on the gate leaves,” Zach says. “I wanted my team to be well-informed, to voice their concerns and ideas, and to have everything they needed to excel.”
Adding another layer of collaboration, Manson made weekly visits to Greenberry’s fabrication site in Vancouver, WA, meeting with Zach and his crew to track progress and resolve any emerging challenges.
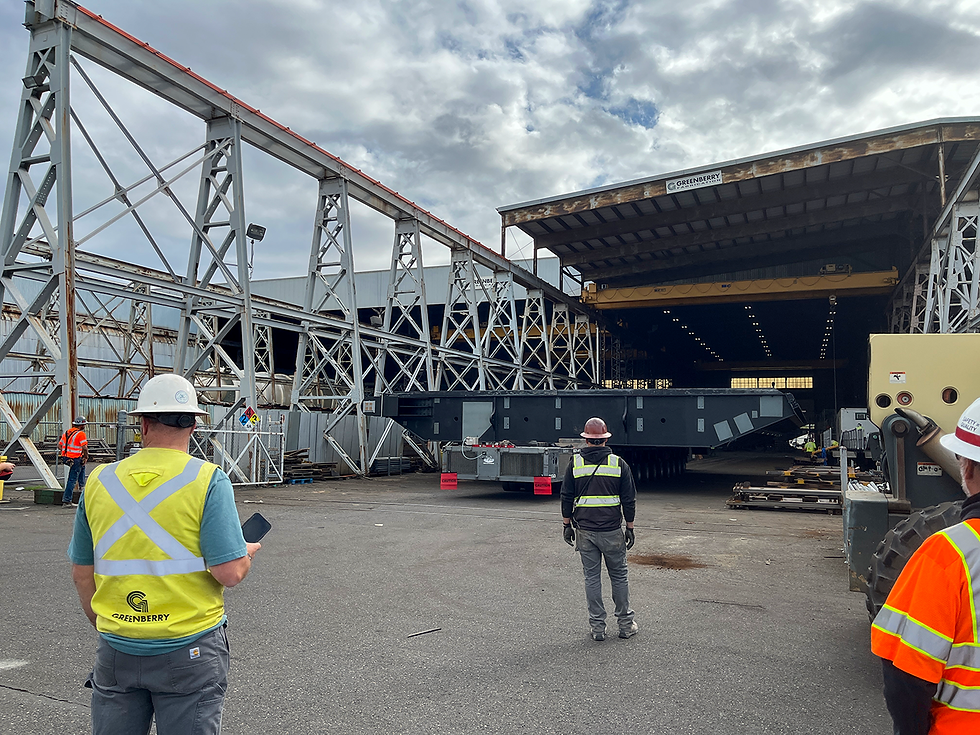
After a year of meticulous weld work and assembly, Greenberry successfully completed the 53-ft by 46-ft gates. The Manson project team coordinated with Greenberry to transport the gates—loading them onto the barge MANSON 73 to be towed by tugboat to Seattle in October 2024.
By November 2024, Manson installed the new gate leaves at the Ballard Locks using DERRICK 24.
Just weeks after the installation, Zach visited the Locks in January 2025, witnessing firsthand the culmination of strategic planning and collective effort between Manson and Greenberry.
“When you’re deep in the work alongside so many people, it’s easy to lose sight of the project’s full magnitude,” Zach reflects. “But standing there, seeing the Locks in full operation, was a powerful reminder that it takes a team to bring a vision to reality.”

留言