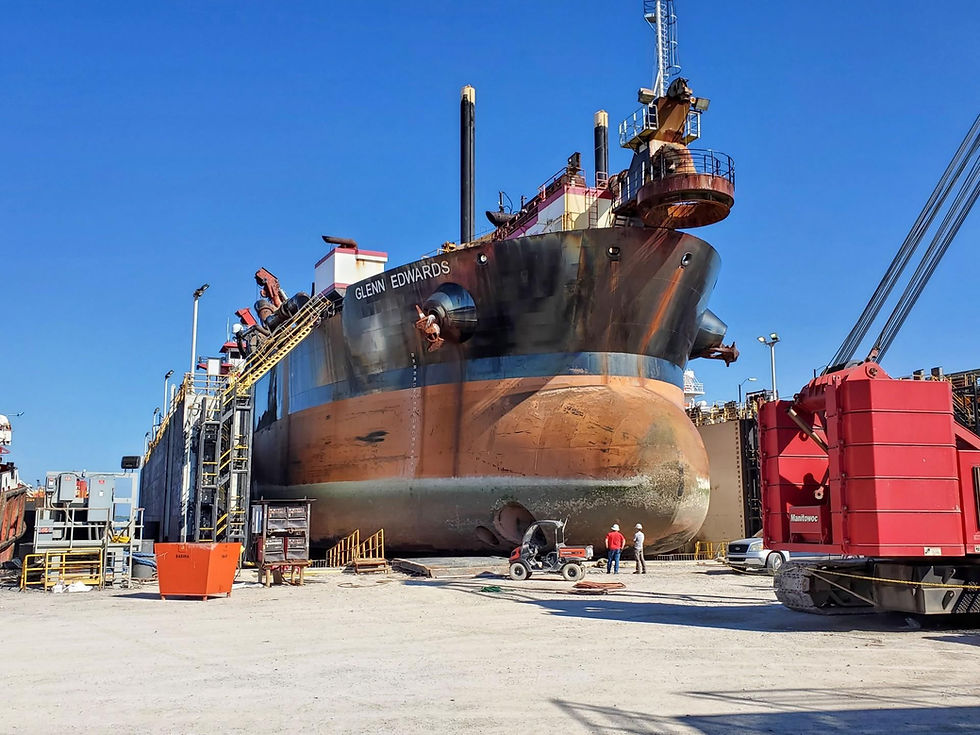
Manson’s iconic red and white vessels can be found working on marine construction and dredging projects across North America. These reliable vessels are one of the company’s prime assets and require routine and regulatory maintenance, often through dry docking, to keep them shipshape. Dry docking is essential to extending the life of the fleet.
Dry docking is the process of taking a vessel to a shipyard for inspection and/or repairs of areas of the ship that are usually submerged. Manson vessels—such as derrick barges, hopper and cutter suction dredges, tugboats, and even flat barges—routinely undergo the process. Much like a car requires regular upkeep to maintain its roadworthiness, maintenance of these vessels ensures they are project ready. Select vessels at Manson must address both preventative and necessary measures to comply with the standards of the United States Coast Guard (USCG) and the American Bureau of Shipping (ABS), both of which require regular maintenance and service.

| Preparations Before Dry Dock
A Manson port engineer and equipment engineer work together to write up technical specifications that ensure Manson vessels undergoing dry dock are compliant with the USCG Code of Federal Regulations as well as ABS regulations. This step is crucial during the preparation phase because it allows Manson to meet ABS load line requirements and receive the USCG Certification of Inspection (COI), permitting the ship to sail from port to port in the U.S.A. This preparation work helps define the shipyard’s scope of work before crews set sail to dry dock.
Next, Manson will remove all tires on the vessel, open hatches and seals, purchase paint, and hire a representative to act as a liaison when the vessel arrives at the dry dock.

Initial Inspection
Members of Manson’s Equipment Department, including the port engineer and equipment engineer, collaborate with Manson’s yard personnel to inspect the vessel and identify areas of the ship that require maintenance and repair. One of the main concerns involves examining the hull to determine if there are signs of structural damage. According to the ABS, the wear and tear of a vessel’s hull components cannot fall below 75% of the ship’s structural integrity. Following the rule of ‘measure twice, cut once,’ Manson often hires a third-party contractor to conduct ultrasonic testing (gauging) to inspect the hull. Gauging includes monitoring the bottom and side shell plating of the hull and the internal brackets and stiffeners.
Depending on the type of vessel and if the ship is classed or requires a COI, the USCG will assist the ABS with the inspection to identify any additional wear and tear to various sections of the ship. Various parts of the vessel are inspected for damage such as bent frames, pitted metal, warped surfaces, and miscellaneous vessel components that need replacement according to the specifications.
At the Dry Dock
Once the vessel arrives at a floating dry dock, shipyard personnel help to navigate the boat into position to sit on top of the keel blocks. With the vessel set in place and anchors hooked to the anchor wires, the water is drained to allow the dock to rise and expose the ship’s hull.
Before the dry dock crew begin work on the vessel, they also perform a thorough inspection of the ship’s hull. The dry dock crew begin work on the vessel by sandblasting the entire surface area of the hull to remove excess material and to identify any fractures. Components like the sacrificial anodes—metal material used to protect the coating of the hull—are one of the main items on the ship that are often replaced.
With structural repairs, crews will work closely with ABS on each section of the vessel that needs fixing. Sections of the hull that have been replaced or fixed are tested for leaks and fractures by both the shipyard crew and ABS. Throughout the dry dock process, personnel from Manson’s Equipment Department remain onsite to keep tabs on the vessel’s progress.


Post-Maintenance Inspection
Manson, the dry dock crew, and the ABS work together in stages to send off the vessel. Cleaning the dry dock is an important stage of the process, as material from the sandblasting, repair, and recoating can cause environmental harm in the water. Once crews wrap up any spillage into the dry dock, Manson conducts a final leak test to ensure the vessel is ready to navigate the waterways.

Comments